In 2004, Aero Craft Japan was founded in what is today Tsuzuki ward, Yokohama. At the time, our main business was manufacturing FRP products—we were still researching the production of carbon racing parts. Using our technological expertise in FRP manufacturing, we combined my experience in vehicle body prototype development with autoclave molding technology to process NC cut molds for all of our design specification data. During this period, we embarked on a number of new endeavors, including the processing of molds for completed carbon parts.
Our current representative director, Takuma Fukatsu, was participating in the All Japan Road Race Championship in 2013, and he officially joined Aero Craft Japan during that time. This marked a period of transformation for all of us, and a greater understanding of racing permeated our entire organization. The world of racing offers great allure. Conversely, it’s also dangerous and rigorous, demanding the capacity for world-class development in an extremely short time at different production sites—each with unique demands. Properly understanding these characteristics is what led us to begin directly receiving orders for racing parts.
As a result, our business completely shifted focus, and we began to focus our energy on creating 100% carbon pre-preg materials through autoclave molding technology.
In December 2016, our M&A with top-level QCD plasterboard mold (used in CFRP molds) manufacturer Fujinami Co., Ltd. marked the inception of today’s Aero Craft Japan, Co. Ltd. Our synergistic relationship allowed for all processes to be completed in-house after reception and verification of layout data, including mold design, NC mold production, fixture production, measurement device production, product fabrication and finalization of inspections. Aero Craft Japan has the capacity to support superior development of in a limited amount of time.
Today we enjoy the continued patronage of our clients—specialist manufacturers inside and outside of Japan that create carbon products for four-wheeled and two-wheeled vehicles, and for industrial use. Our orders received continue to grow daily, and our goal is to continue to develop a system that can produce increasingly high-precision parts on an even tighter schedule. We will contribute value to the world of composite manufacturing by delivering world-class quality products to our customers.
We got to be able to finish the whole process, modeling, producing, and inspecting, by preparing the equipment. We are getting ready the system to live up to customers’ requests.
I hope to continue to try new things with our staff from now on and to make it a good company that manufactures products customers are satisfied with.
Chief executive officer, Takuma Fukatsu
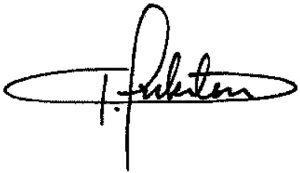
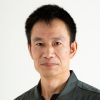
We have many young staff who like making crafts and motorsports. To provide product development along with the requests from customers, we cope with short-term intensive work and challenge new techniques aggressively.
Production Manager, Katsuyuki Okabe
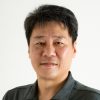
The number of our staff has increased, and we have been able to deal with a large range of requests as we have NC Machine Tools, mold processing, jig manufacturing, and also CFRP product processing we introduced recently. We will aim at a company that can deal with not only existing but also new customers promptly.
Technical Service Manager, Kei Ohkubo